References
Energy generation
New power for the desalination plant
Project location:
Switzerland
Date:
2022
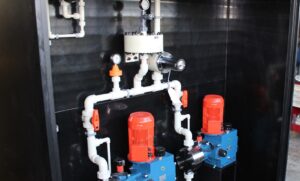
Dosing station for caustic and acids
Systems used:
Dosing stations for caustic soda and sulfuric acid with piston-diaphragm dosing pumps FKM.
Description:
A complete desalination plant with ion exchangers removes dissolved substances from the raw water. The ion exchangers are regenerated by means of acid and caustic. The operator of the nuclear power plant was looking for replacement dosing systemsps for caustic soda and sulfuric acid. The robust design of the dosing pumps and their long operating life were important factors. Of course, the safety and reliability of the dosing systems is very important in a nuclear power plant.
DOSING STATION FOR SODIUM HYDROXIDE FOR THE REGENERATION OF ION EXCHANGERS (ANION EXCHANGERS)
For this project, two redundant piston-diaphragm dosing pumps of the FKM C0 series were installed in a chemical-resistant enclosure made of PE. The transparent splash protection gives high safety to the operating personnel and the environment, while at the same time providing an unrestricted view of the dosing system. Additional safety is provided by the drip tray integrated into the protective cabinet.
The output of the dosing pumps can be adjusted linearly and continuously in the range 0-100% during operation and standstill. The dosing accuracy is better +-1%. The safety valve according to DIN EN 809 is built into the dosing hydraulics and therefore has no contact with the dosing medium.
The selection of high-quality materials enables the safe and reliable operation of the dosing pumps.
DOSING STATION FOR SULFURIC ACID FOR THE REGENERATION OF ION EXCHANGERS (CATION EXCHANGERS)
Two redundant dosing pumps of the FKM series are also used for the sulfuric acid dosing. The protective cabinet in which the chemical dosing pumps are installed is suitable for indoor or outdoor installation (under a roof). In this project, the enclosures were installed in a building. The existing space conditions had to be taken into account during design and engineering.
Treatment of cooling water with CONTINUFLOC solution and dosing system
Project location:
The Netherlands
Date:
2016
Power station (source: wikimedia commons)
Systems used:
Solution and dosing systems CONTINUFLOC with conveyor AIRLIFT for powdery polyelectrolyte, dosing station for polymer solution with piston diaphragm dosing pumps FKM.
Description:
A particular challenge in this project was that the equipment had to be installed and taken into operation at normal operation of the power station, within a very short time.
For the design and installation the restrictive site conditions had to be considered.
Cooling water treatment in a power station
Should surface water be processed to generate cooling water of a power station, it must first be cleaned from impurities. Otherwise these may have negative effects on the pipes, valves and heat exchangers. In a multi-step treatment process this is done through flocculation. In the described project powdery polyelectrolyte was used as flocculation agent.
Preparation of powdery polymer to a polymer solution
The polyelectrolyte from bags is emptied into a floor hopper and lifted by an AIRLIFT loading system into the dry material feeder of the two-chamber pendulum systems CONTINUFLOC.
CONTINUFLOC systems are fully automatic systems for the preparation of granular and concentrated liquid polyelectrolyte. The systems are supplied completely with switch cabinet, wiring and piping and are electrically and hydraulically tested in our factory.
The CONTINUFLOC stand out due to an optimal powder wetting system and provide sufficient maturation time regardless of polymer type or concentration.
Dosing of matured polymer solution
To make from surface water via flocculation cooling water, the matured polymer solution is metered via a dosing station for viscous products. The dosing stations were delivered on skids and completely pre-assembled and tested. For dosing the robust and proven piston diaphragm dosing pumps type FKMV are used, which are specially designed for high viscosity products. The pumps are adjustable 0-100% and have a built-in safety valve.
From planning to commissioning: everything from one source
From engineering to execution and hassle free start-up, the customer has chosen all services provided by Alltech and the systems were ready for use after only a few weeks.
DOSING SYSTEMS FOR WATER TREATMENT IN A POWERSTATION.
Project location:
Keadby/Great Britain
Date:
2013
Systems used: :
Piston diaphragm metering pumps type FKM
Description: :
The Keadby power station in North Lincolnshire, Great Britain works with the dosing technology equipment from Alltech. This project is in conjunction with the upgrading of the natural gas powered power station that will cost the operators approx. 100 million pounds. For the operators of power stations reliability and process security of the dosing equipment are critical factors. Dosing systems are used in several applications such as cooling water, feed water and waste water treatment as well as flue gas cleaning.
MATERIAL SELECTION; ACID AND CAUSTIC RESISTENT.
During the treatment of the feed water in an ion-exchange system in Keadby, acid and caustic dosing skids are used. The chemicals, usually 96% concentrated sulphuric acid and 47% sodium hydroxide are taken from storage tanks. Here the robust piston diaphragm metering pumps type FKM are used. For the dosing heads and diaphragms, caustic and acid resistant materials are used. All metering pumps used have TÜV certified safety valves integrated in the hydraulic. Other safety relevant features are the diaphragm rupture sensors. The stroke length positioning system SERVOSET allows the remote control of the dosing output from 0 to 100%. The dosing systems are installed in a chemical resistant enclosure as the dosing of concentrated sulphuric acid or sodium hydroxide requires a high level of safety for the personnel and the environment.
ACID AND CAUSTIC DOSING FOR THE PH ADJUSTMENT OF RAW WATER.
In Keadby using the Alltech dosing systems, concentrated sulphuric acid is taken from storage tanks and dosed and diluted proportional to the control signal. The diluted chemicals are dosed to achieve a set pH value. For the disinfection of the raw water and the treatment of cooling water Alltech also offers chlorine gas dosing systems.
PE-TANKS, TREATMENT SYSTEMS AND DOSING STATION FOR A BIOGAS PLANT.
Project location:
Münchwilen/Schweiz
Date:
2009
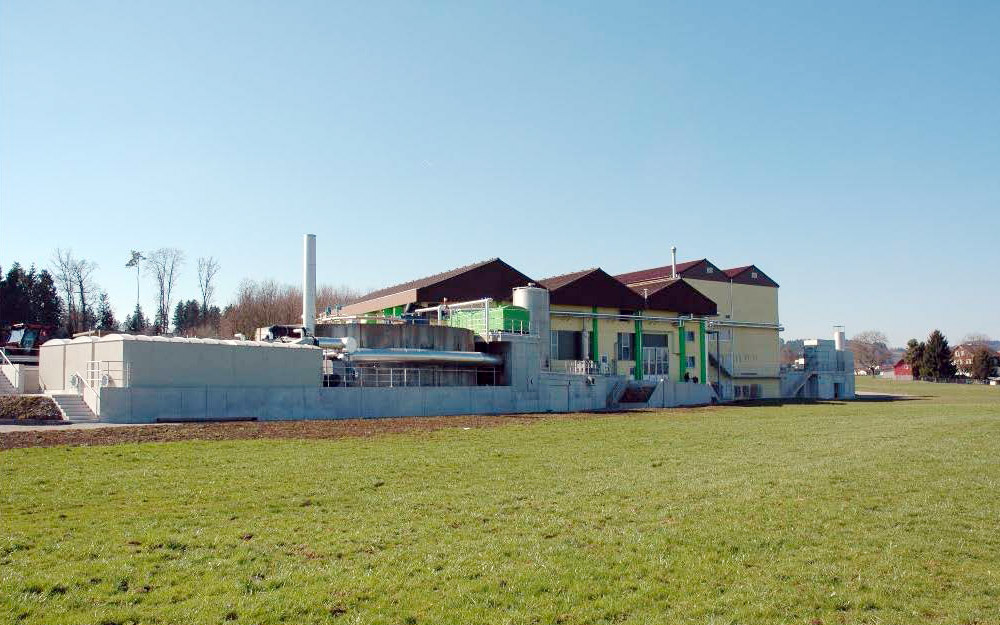
Systems used: :
Various dosing systems including metering technology and on-site control, two-chamber pendulum system CONTINUFLOC
Description: :
Münchwilen is home of a large biogas plant in Switzerland. From 30000 tonnes of organic by-products from the meat industry and other organic waste, approx. 41000 MWh are to be generated from CO2 neutral biogas annually. The project includes the engineering, supply, installation and ininstallation of various dosing systems including metering technology and local control panel as well as diverse thermoplastic tanks in the bio waste fermentation plant.
INDIVIDUAL DESIGN OF THE SYSTEMS FOR THE DOSING OF SPECIFIC CHEMICALS.
The preparation and dosing systems for the chemicals that are used in the biogas plant are designed to meet the different demands of the chemicals (ferric salts, sodium hydroxide, sulphuric acid, defoamers and polyelectrolytes). The certified double-walled tanks are equipped with the corresponding safety equipment. In order to prevent crystallisation, the tanks and dosing lines of the sodium hydroxide station is equipped with trace heating.
THAT CONVINCES: ENERGY EFFICIENCY AND EASY TO MAINTAIN.
In order to achieve the target of a high dry content of the dewatered sludge, a flocculation agent is added to the sludge. The preparation of the polyelectrolytes is done in the proven and reliable two chamber pendulum system CONTINUFLOC from Alltech that also ensures the maturity time required by the specific chemicals. At BIORENDER attention is particularly paid to the robust construction and high reliability of the system. The energy efficiency of the plant was able to equally convince the operators as well as the low maintenance requirement.