References
Food industry
iglo uses mother tanks for the efficient and safe storage of cleaning concentrates.
Project location:
Reken
Date:
2023
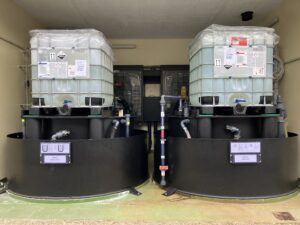
Mother tanks: storage systems for chemicals in IBCs
Systems used:
Mother tank, storage system for the safe handling of standard chemotainers
Description:
iglo has set itself the task of constantly reducing its impact on the environment and is focussing, among other things, on water/waste water management. For the storage of cleaning concentrates, iglo uses mother tanks from Alltech.
TWO MOTHER TANKS ARE USED AT IGLO IN REKEN FOR THE STORAGE OF ACIDIC AND ALKALINE CLEAINING CONCENTRATES.
Product residues in production facilities in the food industry consist of greasy residues, product deposits and mineral residues.
To ensure hygienic production and clean batch changes, product residues are removed within the plants using CIP ‘cleaning-in-place’ in validated cleaning processes. iglo uses mother tanks at the production plant in Reken, Westmünsterland, for decanting from IBC delivery containers and for storing the acidic and alkaline cleaning concentrates.
The cleaning concentrates are automatically dosed from the mother tanks into the production plant’s CIP system using a pipe, feed pump, volumetric flow meter and control valve to produce the working solutions
HYDROCHLORIC ACID FOR THE PH NEUTRALISATION OF ALKALINE DEVIATIONS IN THE FACTORY WASTE WATER.
IBCs (Industrial Bulk Containers) with hydrochloric acid are positioned directly on the container using a forklift or lifting device and emptied completely into it. This ensures a continuous supply to the chemical dosing system and the time of the transfer process does not have to be monitored precisely. The hydrochloric acid is conveyed from the mother tank into a ring line, from which alkaline deviations in the factory waste water are corrected at three different local positions within the iglo waste water pre-treatment system using a pH control algorithm.
Modernising the company-own waste water treatment of a cheese manufacturer.
Project location:
Schongau
Date:
2013
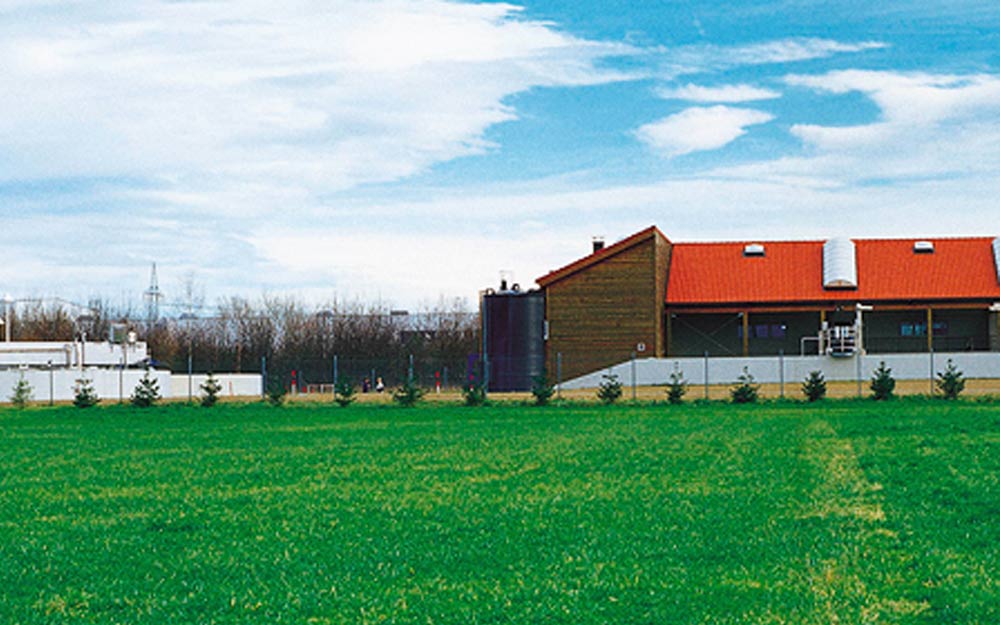
Systems used:
CONTINUFLOC 2000 and 1000
Description:
The Schongau works of Hochland Deutschland GmbH is one of the most prominent production plants for cream cheese and soft cheese in Europe. Hochland works, as does Alltech, with a strong focus on quality. At Hochland environmental protection is strongly anchored. The target, for example, is to minimise environmental damage and the use of chemicals in the company’s own waste water treatment plant. Here production waste water with a pollution load of approx. 38000 EW is treated.
ALLTECH CONTINUFLOC SYSTEMS 2000 AND 1000 INSTALLED SINCE 1999 AT HOCHLAND.
The initial contact between Hochland and Alltech took place in 1999, shortly after the then newly constructed works started operation. For dewatering sludge, Alltech supplied the preparation and dosing system CONTINUFLOC 2000 and for subsequent elimination the CONTINUFLOC 1000. As both systems operated across all the years without fail and supplied an optimum product quality of polymer concentrate, it was an easy decision for the Hochland manager of the waste water treatment plant Mr Richard Schuster, to contact Alltech for the conversion of the phosphate elimination system in May 2012.
INSPECTION AND OPERATING COSTS REDUCED, OPERATING SAFETY INCREASED.
The phosphate in the waste water of the creamery is chemically eliminated. To eliminate phosphate, ferric III chloride sulphate is stored in a 30 m³ tank. Alltech retrofitted this existing tank with a new suction line including an automatic priming system. This has the advantage for the waste water treatment personnel that from then on there is significantly less inspection and operating work and the operational safety is increased. The discharge system on the storage tank is completely installed in a protective housing so that also in winter it is protected from frost and the weather. The space for the dosing station was limited to two by two metres. Alltech supplied a tailored system that corresponds both to the available space and the requirement that the existing control centre can be used.
FKM PISTON DIAPHRAGM METERING PUMPS FOR THE GREATEST SAFETY AND PRECISION.
The dosing station is equipped with durable diaphragm metering pumps from the FKM range. The overpressure safety valve is already integrated in the hydraulic system of these pumps. These metering pumps meet the highest standards for operating standards and precision. The reaction products from elimination are removed with the sludge for the treatment plant and disposed of. The waste production water from Hochland is cleaned with an efficiency of 99% regarding the organic content and nutrients and is piped directly into the River Lech.